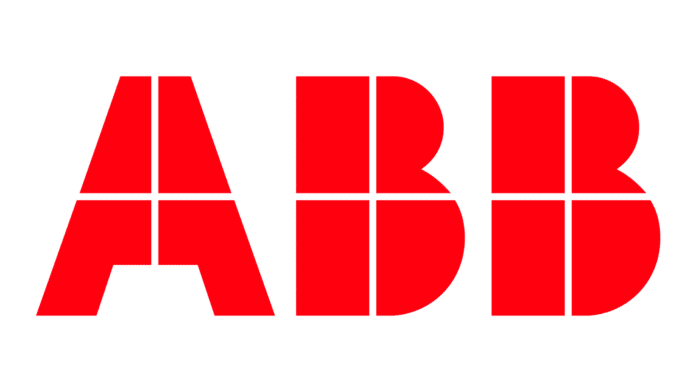
ABB India has announced that it has secured an order from Reliance Life Sciences (RLS) to deploy automation and control solutions for their new biosimilars and plasma proteins manufacturing facilities in Nashik, Maharashtra. RLS is expected to lower the total cost of ownership by adopting ABB’s DCS running on the most recent Windows version.
The implementation of ABB’s DCS in a virtualized environment is expected to enhance project efficiency by simplifying server management and reducing operational costs. ABB India in an exchange filing on August 21 announced that it has secured an order from Reliance Life Sciences (RLS) to deploy automation and control solutions for new biosimilars and plasma protein manufacturing facilities in Nashik, Maharashtra.
The scope of the project involves complete automation of manufacturing processes through ABB’s distributed control system (DCS) ability system 800xA. This cutting-edge solution encompasses Remote I/O systems, Batch Recipe Management, and MES integration. By harnessing ABB’s advanced technology, RLS aims to enhance its manufacturing processes, meet regulatory standards, and elevate the quality of its products.
The integration of ABB’s DCS operating on the latest Windows version provides a multitude of benefits for RLS. The deployment of this advanced system allows for a reduction in the total cost of ownership. Additionally, the DCS solution acts as an integration platform, facilitating real-time monitoring of various plant sections and optimizing maintenance processes. The technology shall additionally enable streamlined data communication, minimises wiring, optimises hardware footprint, and accelerates project execution.
The 160-acre Nashik facility is set to house manufacturing plants for a range of products, including plasma proteins, biopharmaceuticals, oncology pharmaceuticals, and vaccines. Given the intricate nature of large-scale biotechnology production and the strict adherence to regulatory guidelines, ABB’s System 800xA solution proves vital in minimising manufacturing errors, ensuring consistent product quality, and offering seamless operator interaction and batch control.